Stainless steel pipe fittings are essential pipe connectors made from high-quality stainless steel, used extensively in various pipeline systems. They are widely employed in industries such as petroleum, chemical processing, papermaking, and electric power. This comprehensive guide introduces the relevant information about stainless steel pipe fittings, covering materials, common types, and manufacturing processes, ensuring you select the right fittings for your projects.
Materials Used in Stainless Steel Pipe Fittings
The primary material for manufacturing stainless steel pipe fittings is, unsurprisingly, stainless steel. Stainless steel offers exceptional durability, corrosion resistance, and reliability, making it ideal for demanding industrial applications. The most commonly used grades include 304, 304L, 316, and 316L stainless steel. Each grade has unique properties tailored to specific environments and requirements.
304 Stainless Steel
304 stainless steel is renowned for its excellent corrosion resistance and good mechanical properties. It is highly formable, making it ideal for manufacturing high-quality pipe fittings used in general-purpose applications.
304L Stainless Steel
304L stainless steel is an ultra-low carbon variant of 304 stainless steel. With a lower carbon content, it offers enhanced corrosion resistance, especially in welding applications, making it suitable for environments where welding is required.
316 Stainless Steel
316 stainless steel includes molybdenum, which significantly improves its resistance to chlorides and enhances overall corrosion resistance. This makes it particularly suitable for marine environments and systems exposed to harsh chemicals.
316L Stainless Steel
316L stainless steel is the ultra-low carbon version of 316 stainless steel. It provides superior resistance to chlorides and maintains stable performance even in highly corrosive marine environments, ensuring longevity and reliability.
Common Types of Stainless Steel Pipe Fittings
Stainless steel pipe fittings are categorized based on the type of fitting and the connection method. Understanding these categories is essential for selecting the right fittings for your pipeline systems.
Based on the Type of Pipe Fittings
Elbows
Elbows are used to change the direction of the pipeline system, typically available in angles of 45°, 90°, and 180°. Special cases may include 60° elbows. They can be connected to pipelines through welding, socket type, threaded connection, or flange connection, resulting in welded elbows, butt-welded elbows, stamped elbows, etc.
Elbows are primarily used to connect pipes of the same or different nominal diameters, facilitating changes in direction within the pipe. Common applications include water pipes, heating systems, gas pipelines, and fire protection systems.
Tees
A tee is a pipe fitting with three openings—typically one inlet and two outlets or two inlets and one outlet. Also known as a three-way pipe fitting or a three-way joint, tees are available in T-type and Y-type configurations. They are mainly used to change the direction of the fluid within the pipeline or to divert fluid from the main pipeline to different directions.
Tees can connect pipelines of the same diameter or different diameters, resulting in equal-diameter tees and reducing tees.
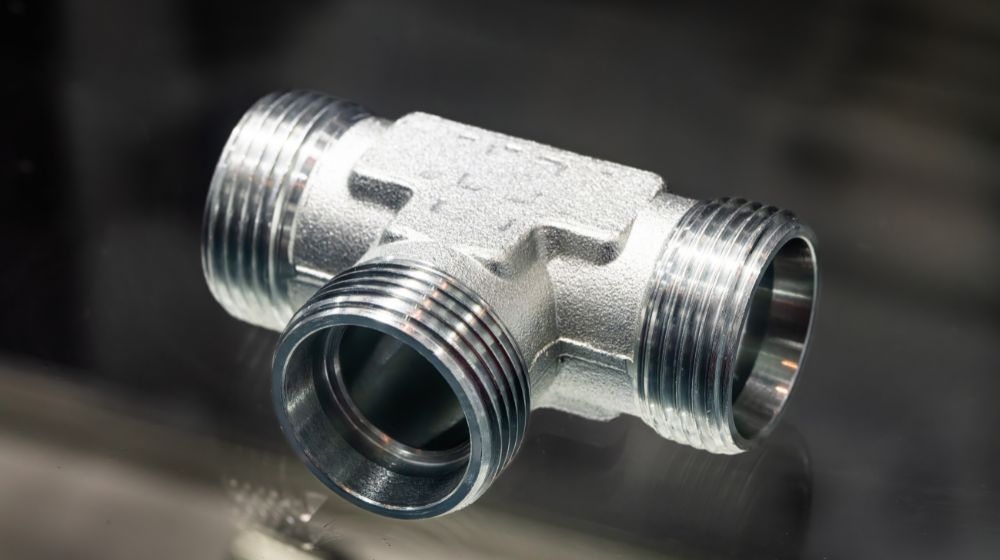
Cross-Way
The cross-way is similar to the tee but designed to connect four pipelines, enabling fluid dispersion and convergence in four different directions. Its main body includes four connection ports, providing more versatility in pipeline direction than a tee.
Cross-ways are predominantly used in industries such as petroleum, natural gas, and chemicals, where complex fluid routing is required.
Plugs
Plugs serve as sealing components in pipeline systems, preventing leakage and maintaining system stability. They are used to temporarily or permanently seal pipeline openings. Plugs can be customized in size and specifications to fit various pipeline systems.
In pipeline systems, plugs are crucial for preventing leaks, avoiding external pollution, and ensuring smooth operation. They are widely used in chemical and petroleum industries.
Pipe Caps
Pipe caps, also known as end caps, are used to close the ends of pipes in pipeline systems, preventing leakage. They ensure the closure, integrity, and safety of the pipeline system.
Pipe caps come in various types, such as round pipe caps and hexagonal pipe caps, each with unique characteristics and advantages. Selection depends on the specific use environment and industry requirements.
Based on the Connection Method
Stainless steel pipe fittings can also be categorized based on their connection methods, which include welded, threaded, and flange connections.
Welded Pipe Fittings
Welded pipe fittings involve joining the fittings to the pipes using welding techniques such as butt welding or socket welding. Butt welding involves adjusting the angle between two pipes and welding them together, while socket welding requires inserting the pipe into the fitting before welding.
Threaded Pipe Fittings
Threaded pipe fittings connect stainless steel pipes and fittings through threaded connections. Common thread types include NPT (National Pipe Thread) and BSP (British Standard Pipe).
NPT threads adhere to the US National Pipe Thread Standard and are widely used in the US market. BSP threads follow the British Standards Institute guidelines and are available in BSPT and BSPP types, predominantly used in Europe and Commonwealth countries.
Flange Connection Pipe Fittings
Flange connection pipe fittings are commonly used in industrial pipelines due to their ease of disassembly and strong connection. They can withstand high temperatures and pressures, making them suitable for sectors such as petroleum, chemical industry, and natural gas.
Manufacturing Process of Stainless Steel Pipe Fittings
The manufacturing process of stainless steel pipe fittings involves several meticulous steps to ensure quality and precision. The primary processes include forging, casting, welding, and precision casting.
Forging
Forging is the process of plastically deforming metal using a forging machine to form the desired shape and size. Although complex and costly, forging enhances the strength of the metal, resulting in high-quality pipe fittings.
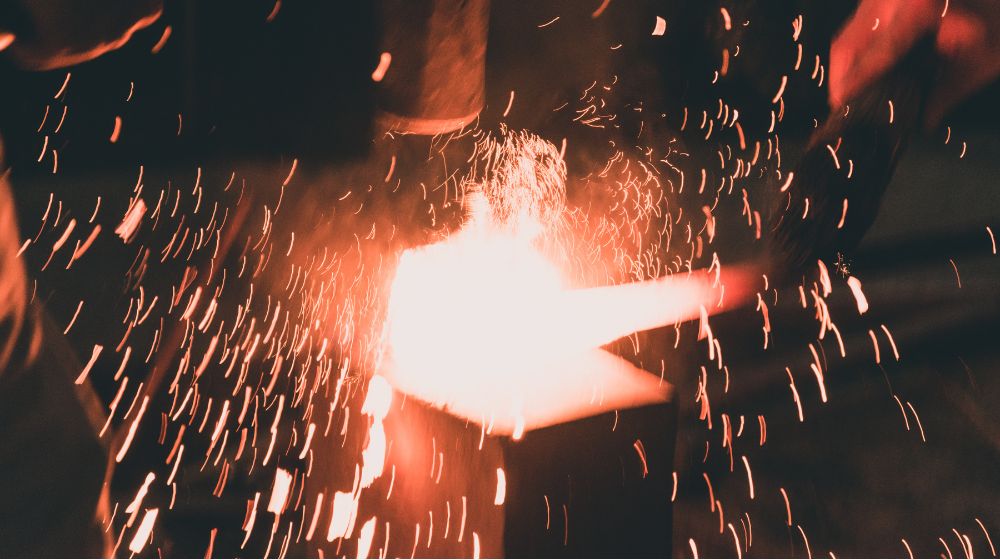
Casting
Casting involves pouring molten stainless steel into a pre-prepared mold and allowing it to cool and solidify. This process is cost-effective for mass production and can create complex shapes with precision.
Welding
Welding joins two or more parts together by applying heat, ensuring a stable and sealed connection. Common welding techniques for stainless steel pipe fittings include TIG and MIG welding, which provide strong and leak-proof joints.
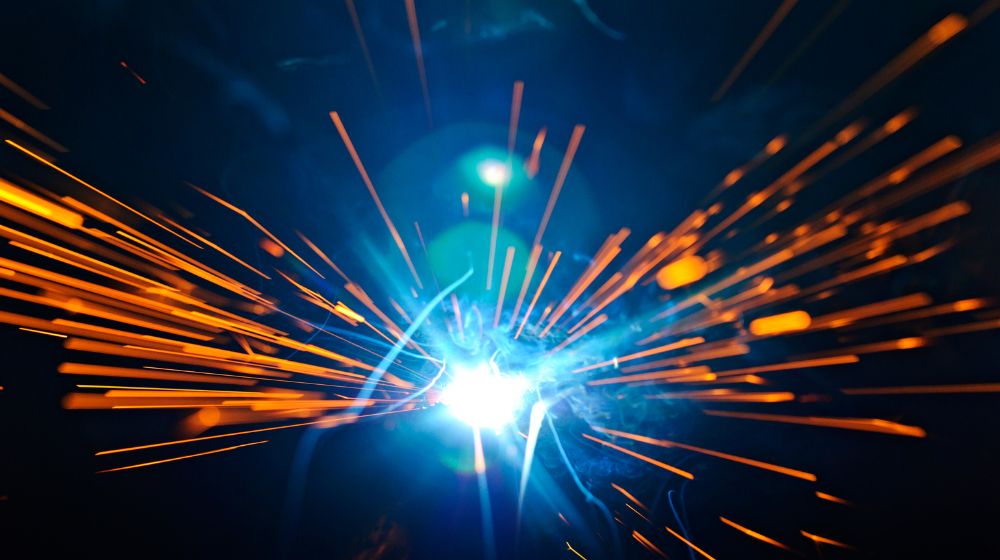
Precision Casting
Precision casting produces pipe fittings with higher precision and better surface quality. This process is ideal for applications requiring strict specifications and superior product finishes.
Applications of Stainless Steel Pipe Fittings
Stainless steel pipe fittings are utilized in a wide range of industries due to their robustness, corrosion resistance, and versatility:
- Oil and Gas: Transporting hydrocarbons and ensuring leak-proof connections.
- Chemical Processing: Handling corrosive substances with high resistance.
- Food and Beverage: Maintaining hygienic standards for sanitary applications.
- Water Treatment: Durable against various water qualities and treatment chemicals.
- Construction: Plumbing systems for residential and commercial buildings.
Frequently Asked Questions (FAQ)
What are the benefits of stainless steel pipe fittings?
Stainless steel pipe fittings offer exceptional durability, corrosion resistance, and high-temperature tolerance, making them suitable for demanding applications across various industries.
How are stainless steel pipe fittings manufactured?
They are manufactured through a multi-step process involving material selection, cutting and shaping, forming and welding, and finishing and quality control to ensure precision and reliability.
What industries use stainless steel pipe fittings?
Industries such as oil and gas, chemical processing, food and beverage, water treatment, and construction extensively use stainless steel pipe fittings for their superior performance.
How do I choose the right type of stainless steel pipe fitting for my project?
Consider factors like fluid type, pressure and temperature conditions, corrosion resistance requirements, and system design. Consulting with a specialist can help in selecting the most appropriate fittings.
Contact Us
At ProCam Lock, we are committed to providing high-quality stainless steel pipe fittings tailored to your specific needs. Whether you require detailed specifications, custom solutions, or expert advice, our team is here to assist you.
Contact us today to find the perfect stainless steel pipe fittings for your project and ensure optimal performance and longevity.
For more information on industry standards, visit ASTM International, which outlines the necessary specifications for high-quality stainless steel pipe fittings.
Explore more about our types of pipe fittings and how they can benefit your projects.
Learn about our contact options to get personalized assistance and support from our experts.
Stay updated with the latest trends and advancements in pipe fitting technologies by visiting our blog.
Enhance your pipeline systems with our top-tier stainless steel pipe fittings and experience unmatched quality and performance.