Do you want to know how the stainless steel camlock that runs smoothly in your transmission system and equipment is made? What rigorous processes and strict tests does it go through?
If the answer is yes, you will get the information you want from this article. You can learn about the manufacturing process of stainless steel camlock from the following 16 steps and get the answers to your questions.
Step 1: Customize the Mold
First, customize the mold. An excellent product comes from a high-quality mold. A standard high-quality mold will not produce a bad product.
Therefore, the design of the mold is crucial. It is the basis of everything. It needs to be confirmed by multiple parties before other processes can be continued. If the mold manufacturing does not achieve good results, it needs to be remade until a high-quality mold is manufactured.
Therefore, it is necessary to first customize the appropriate mold according to the drawing, and only after the mold is manufactured can the next process begin.
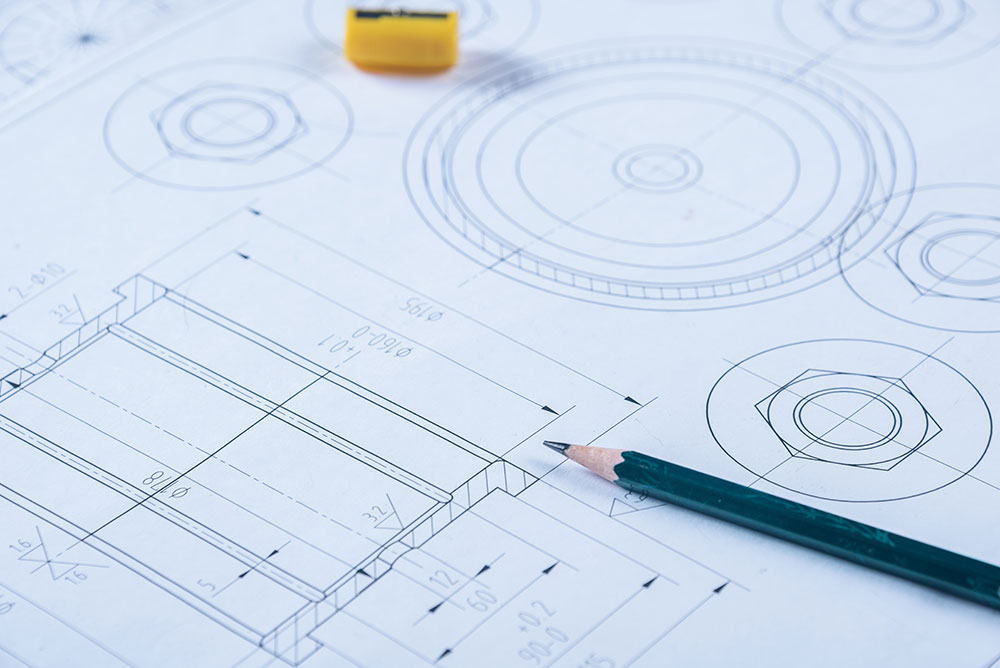
Step 2: Wax Mold Injection
Wax Mold Injection is a very important step. After making the mold, you need to preheat the mold to ensure that the wax can flow evenly and fill the entire mold. Then, the next step is to start wax mold injection.
Wax Mold Injection mainly uses high-quality stable medium-temperature wax, and the ambient temperature is stable at 24-26℃. Because wax has certain requirements for the environment, it will deform if it is too hot, affecting product quality and production efficiency.
Semi-automatic machines can be used when the manufacturing quantity is small, and fully automated machines must be used when the batch quantity is large. The use of automated machines can accurately control the manufacturing process of the product to ensure that there are no accidents in the production process.
The wax enters the mold through an automated machine, evenly filling the mold and gradually forming a wax model. When a complete wax model is formed, this step is completed.
Step 3: Wax Mold Repair
After wax mold injection, you may find that there is a problem with the connection between the molds, affecting the shape or aesthetics of the product, or there is excess wax poured into other places or overflowing. At this time, the wax mold repair process is needed.
The wax mold repair will repair any problem areas or remove any excess wax to ensure the quality and integrity of the product. After this, the product will be inspected for bubbles, cracks or obvious defects.
Step 4: Wax Mold Welding
Different product structures and product designs have different arrangements, some are placed horizontally, and some are placed vertically.
Generally, a specific wax mold welding project will be designed based on the structure and characteristics of the product, such as how many pieces are in a string and how they will be arranged. These will be clearly written out so that they can be used as a standard reference for the manufacturing process.
Step 5: Mold Making
In the process of mold making, zircon sand and zirconium powder are generally used as mold making materials, which are mixed in a certain proportion to form a viscous and high-temperature resistant slurry. Then the wax mold is immersed in the slurry to evenly cover the surface of the wax mold.
After that, the wax mold coated with slurry is placed in the drying room for drying. Each drying room is kept at a constant temperature and humidity for 24 hours to ensure that the product can be effectively dried. Different drying rooms have different temperatures.
Next, the slurry coating and drying process are repeated until the thickness of the mold reaches the specified standard.
Step 6: Dewaxing
After the mold is made, the dewaxing step is carried out.
This step needs to be completed in a dewaxing kettle. Put the mold into it, keep the ambient temperature at high temperature and high pressure, wait for the wax mold in the mold to melt and flow out, and the mold is left.
Step 7: Pouring
Pouring is also a very important step.
First, put the mold into the natural gas roasting furnace and heat it to about 1000 degrees. Then heat the steel material to about 1600 degrees at the same time. After the steel material is heated to the required level, start pouring.
This step has certain risks, so pay attention to the safety of the staff.
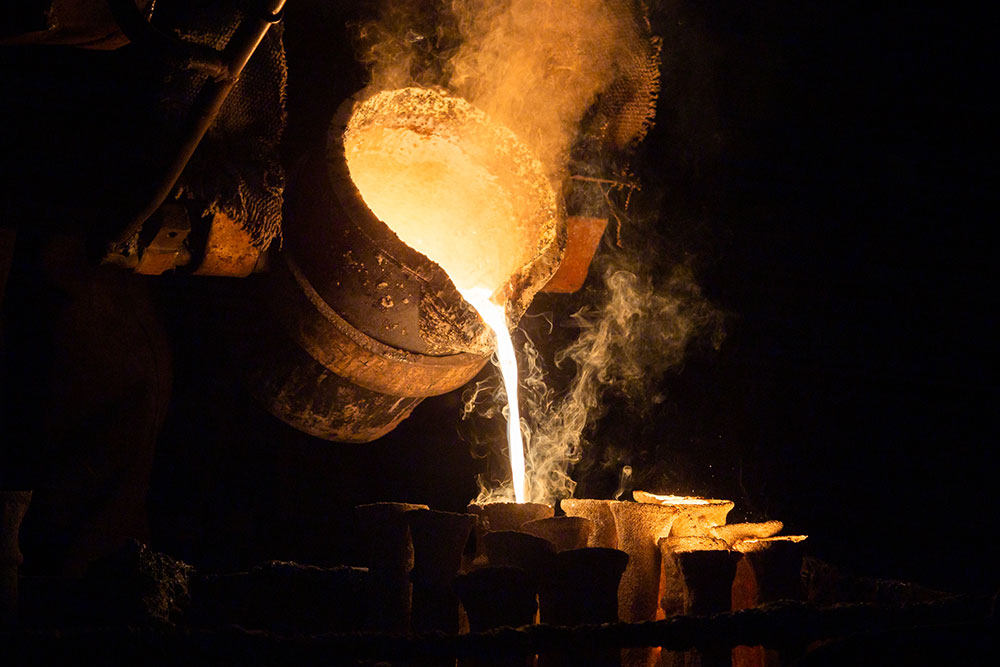
Step 8: Lost Pattern
After the cast is cooled and solidified, a rough blank is obtained.
The next step is the lost pattern. Use a shell breaker to break the mold and take out the stainless steel casting inside. This is a product blank.
Next, this product blank will be processed and refined to gradually become a precise and high-quality stainless steel camlock.
Step 9: Cutting
During the pouring process, some essential pouring gates and risers will be formed.
The pouring gate refers to the channel for molten metal to enter the casting, and the riser refers to the supplementary part added during the metal casting process to prevent material shrinkage.
This part is essential in the manufacturing process, but it is not necessary in the final product. Therefore, these pouring gates and risers need to be cut away and separated from the manufactured product to ensure that subsequent processing is not disturbed.
Step 10: Grinding
After cutting, uneven parts will form on the product surface and in areas such as pouring gates, which may be burrs, protrusions, etc. These will affect the flatness, smoothness and integrity of the product.
Therefore, grinding equipment is needed to grind these uneven areas flat so that the next step can be carried out.
Step 11: Pickling
This step requires the use of an acidic solution to react chemically with the metal oxide on the surface of the product to remove the oxide layer on the surface of the product blank, making the surface of the product blank relatively smooth.
Step 12: Shot Blasting
After pickling, the shot blasting process can be carried out.
Shot blasting refers to the use of high-speed rotating steel shots to remove the oxide layer residue, steel slag debris and rust on the surface of the product blank, so that the product blank gradually turns into the original color of stainless steel.
This is the final product blank.
Step 13: Inspection and Storage
The finished product blanks need to undergo multiple inspections to ensure that they meet the standards and specifications before they are officially put into storage.
Step 14: CNC Machining
After the product blank is formed, further processing procedures are required.
CNC machine tools are needed to polish and refine the product’s size, accuracy, thread and other more detailed data to optimize and improve the quality and accuracy of the final product.
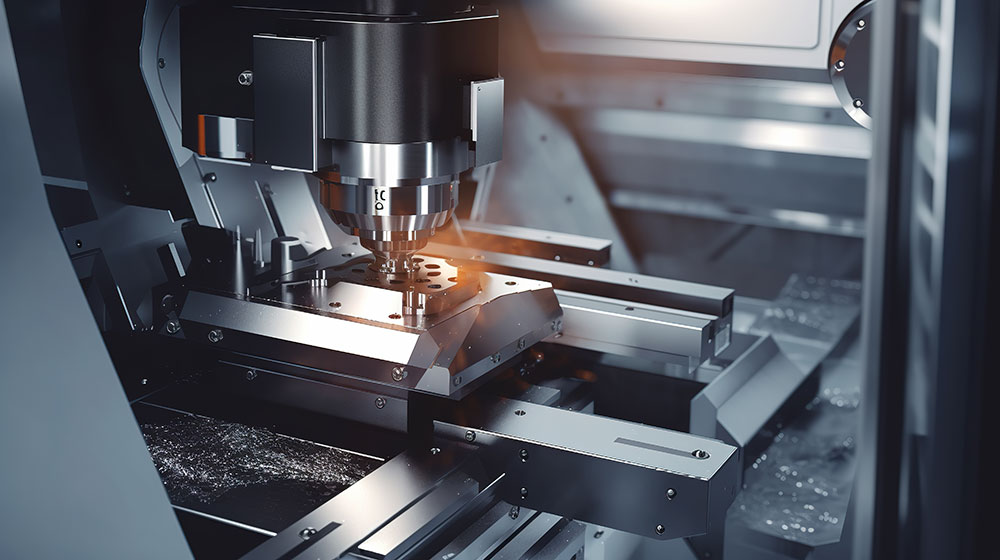
Step 15: Finished Product Storage
At this step, the product is basically manufactured and after a series of precise inspections and tests, the finished stainless steel camlock is stored in the warehouse.
This step of the process mainly uses various inspection instruments and equipment to inspect the product’s size, thread, angle, completeness, etc. The finished product’s air-tightness and service life will also be strictly tested to ensure that the product meets all standards.
Step 16: Packaging and Shipping
Finally, appropriate and reasonable packaging is carried out according to the customer’s order quantity and packaging requirements.
After everything is ready, the product will be shipped.
Conclusion
The above is the 16-step manufacturing process of stainless steel camlock.
After reading this article, most of your questions should have been answered, and you should have a certain understanding of the manufacturing process of stainless steel camlock.
If you have any other questions or want to know more relevant information, you are always welcome to write to us.